I don’t know if you’re familiar with Annihilator broadheads, but they’ve come out with some really crazy new technology that has worked very well on the 3-blade broadheads that they’ve made.
And, you can check out the tests on other Annihilator heads that I’ve done. They have a few different models and now, I’ve got another one… the Katana!
I was talking to the Annihilator crew at the 2025 Archery Trade Association show in Indianapolis. During that conversation, I saw this brand new head that they were working with and hoping they have ready by Spring 2025.
And they did!
For all the testing, I used my Elite Bows. And then for the flight testing, I used a Killer Instinct Crossbow because I can just put it on a tripod and really get it steady and there is so much less human error involved in the accuracy. The only difference flight to flight is the broadhead that’s screwed on to the tip of the bolt. Then, for all the arrows and bolts, I’m using Bishop Archery products.
First things first… I love the name “Katana.” It refers to a Japanese sword.
I’ve got a couple Katanas from Japan actually, as I worked in the Ministry over in Asia for a number of years, and had some friends in Tokyo.
But this Katana is a broadhead. And man, this is one wicked cool broadhead!
So, I was really eager to introduce it to you, go through some of the design features and specifications, and then put it to the test. Let’s see how it fared (buckle up!)
The Annihilator Katana Broadheads Up Close
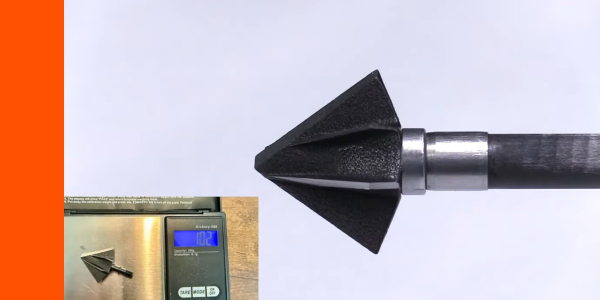
So, here’s a good look at the Katana. And man, this broadhead is loaded with innovation! You may think, “Okay, just another 2-blade broadhead.” It has a 2-blade base, but there is just so much more going on!
First of all, let’s start with the materials. Beginning in 2025, Annihilator began using a brand new, proprietary steel in all their heads.
Annihilator has compared their steel that’s used here in the Katana to D2 to S30V to A2 and to S7 tool steels. They showed that in every category that they quantified, (toughness, edge retention, durability, sharpness, and ease of sharpening), that it either equaled or exceeded all those other steels. So, in their mind, it’s way better than any other steel that has ever been used in a broadhead application. Pretty bold claim there. Below, we’ll see how it performed in the tests.
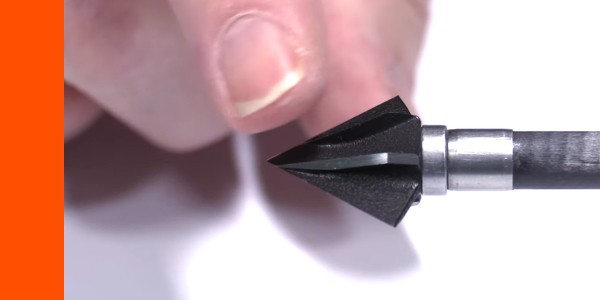
The Katana has a tough, black coating.
The Katana broadhead is coated with a black nitride coating. It’s different than black oxide. It’s much better, apparently, at corrosion resistance compared to other broadheads.
N1 Shirts just for bowhunters!
-
N1 Outdoors® Bareback Bowhunter™ Tee
$28.99 – $32.99 -
N1 Outdoors® “USA Antler” Tee
$24.99 – $28.99 -
N1 Outdoors® Angry Arrow™ Tee
$24.99 – $28.99
Katana Dimensions and Cut Size
In terms of the dimensions, the 100-grain model has a 1-inch cut. (It also comes in 125 grain model and a 200 grain model). In the 100 grain model, the overall length is 0.76″. In the 125 grain model, it has the same base but it’s a little bit longer. And then the 200 grain model, it has got a 1.25″ base and it’s a little bit longer. It’s a beast!
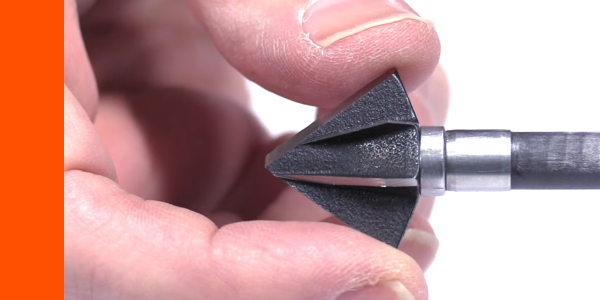
The Katana has a 1″ width cut…
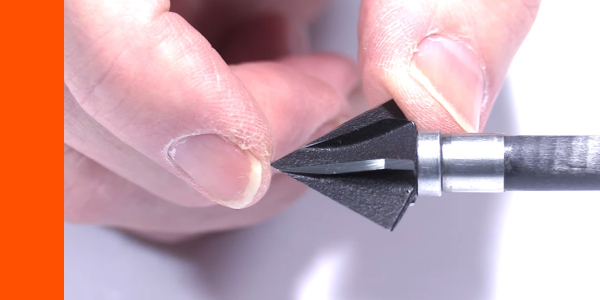
and an overall length of .76 inches.
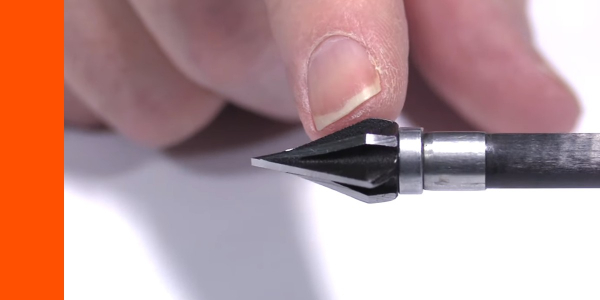
All sizes are solid (no venting). But , it has 6 blades to it, which is really interesting. It has these single bevel blades on the outside there (I believe they are a 40-degree angle, but I’m not exactly sure.)
And then, instead of just having a thick ferrule to open up a hole for the arrow shaft to go through, they put in two more single bevel blades on each side. And, in doing that, they created more cutting surfaces and reduced the friction that comes with a material pressing against the flat surface of a broadhead. So, it just creates more cutting areas to cut more tissue.
And then, these are single bevel sharpened as well, but not in the same direction. They kind of just angle towards each other.
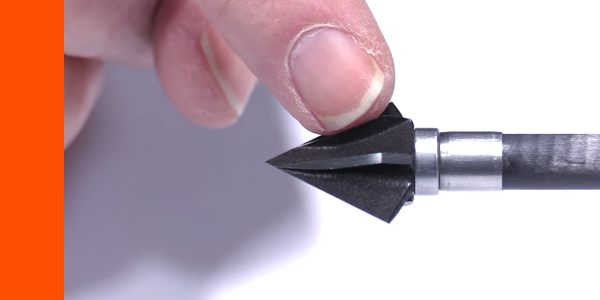
Another unique feature of the Katana is the three “scoops” per side that are created by the extra blades.
These blades create three “scoops.” And, then the same thing on the other side. These are the scoops that the Annihilator became known for, and they call it their cavitation technology that not only aids in flight, like the dimples of a golf ball as it rotates, but, it also creates a pressure inside the cavity of an animal, a forward pressure and a pressure behind it that creates huge tissue displacement. That’s their claim, and they’ve got some incredible photos to show it.
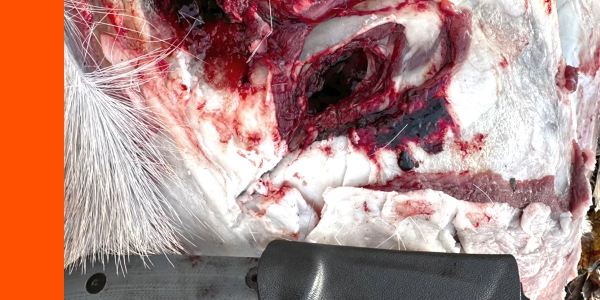
I saw this one photo that was sent to me of a deer, and you can see the size of the hole that it put there in the deer. That’s an 8-inch knife next to it, compared to this 1 inch cut broadhead. But apparently, they just open up a really big hole. I suppose it depends on what angle you hit it at, but it has the potential to open up a really big hole.

And then in terms of thickness, the blades are really interesting. I took some pictures to try to highlight it. In the front, the blade is 0.060″ thick.. And then towards the rear, it gets more narrow. And, that just adds more weight forward and more durability forward for that hard impact and then they saved some weight as they go back and it gets a little bit thinner there in the back.
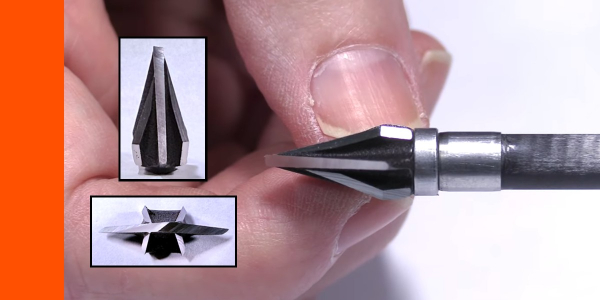
This gives you an idea of the blade thickness of the Katana 100 grain.
So man, just so much going on! A total cut of 1.74″ given these 6 cutting edges, one inch one way, and two that are 0.37″ the other way.
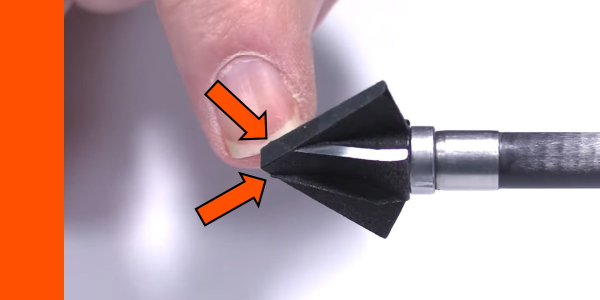
The blades not only open up a bigger hole to allow the arrow to glide through it to reduce the surface friction, but they also provide lateral support to this 2-blade broadhead, not unlike a ferrule that goes all the way to the tip. And, you notice they go all the way to the broadhead tip and almost create a little dimple.
Now, in terms of resharpening, these little back blades, you just resharpen with a small file and just do your best. They’re single bevel, so they shouldn’t be that hard. It’s not that crucial for them to be razor sharp. But there’s a new Stay Sharp Guide sharpener called The Answer that would work really well on this. It works really well on a lot of different broadheads, but it would do a great job sharpening these edges.
Katana Broadhead Testing
This head looked so innovative and interesting, that I was curious to see if it was just a bunch of gimmicks, or if Annihilator was really on to something special…
Flight Test
I shot one 1 field point and then one broadhead @30 yds with a Killer Instinct SWAT X1 Crossbow 675 gr Bishop Bolt, at 300 fps
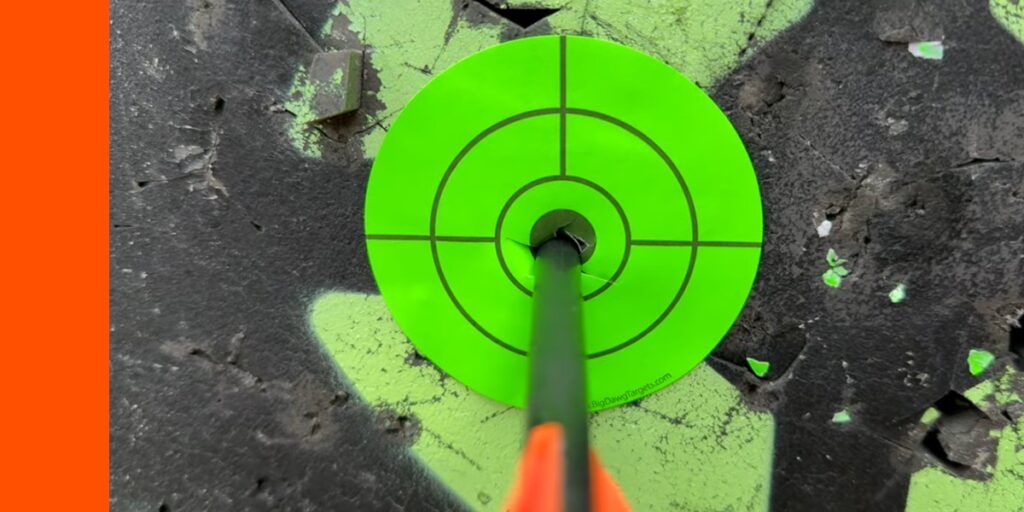
The Katana crushed the bullseye!
Edge Test 1 Initial Sharpness Test
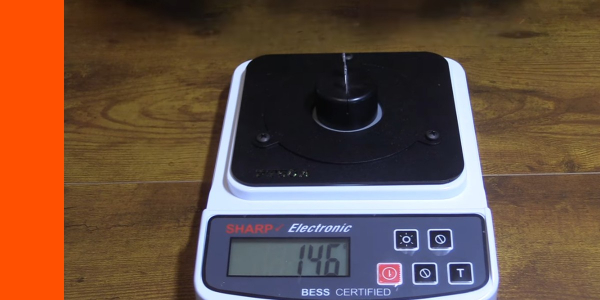
It took 146 grams of force to cut through the polymer wire, which is a 10 on a 10-point scale plus a bonus for being under the threshold of 200.
Penetration Test 1
I shot the Katana broadhead into Clear Ballistics FBI Gel, fronted by a 2/3″ Rubber Foam Mat and 1/2″ MDF.
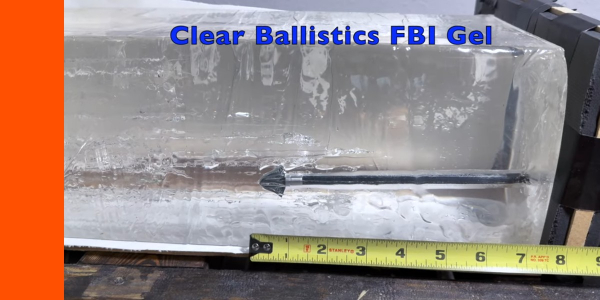
It penetrated 9″ which is a 10 on a 10-point scale.
Edge Test 2, Edge Retention Test (Sharpness after Penetration Test 1)
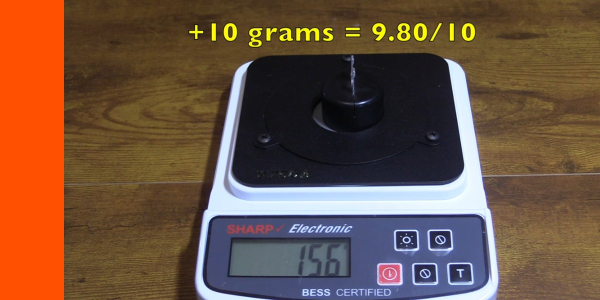
It only took an additional 10 grams of force to cut through the wire, which is a 9.8 on a 10-point scale. And it also got an extra bonus for both the sharpness and the edge retention being under the threshold of 200.
Penetration Test 2 (Layered Cardboard)
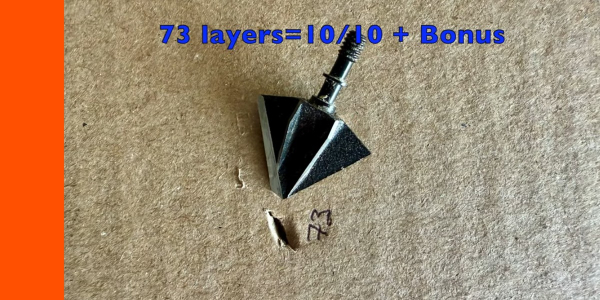
The Katana penetrated through 73 layers, which is a 10 on a 10-point scale plus a bonus for being over the threshold of 70. And, it’s the first broadhead ever to penetrate through more than 70 layers! And, on top of that, it’s the first broadhead ever to reach the maximum of 9″ of penetration and 70 layers of penetration in both of the two penetration tests. So it gets an extra bonus for that!
Rotation (Clear Ballistics FBI Gel)
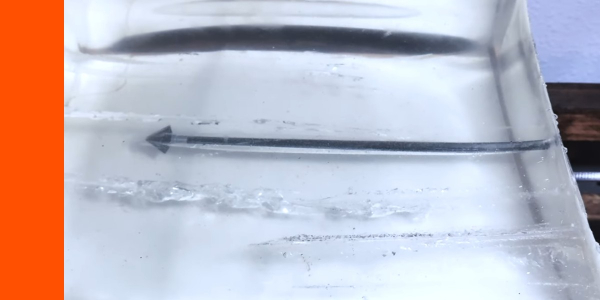
The Katana rotated a whoping 88 degrees at 12″. Man, that is an impressive wound channel right there!
Durability Test (3 shots into 1/2″ MDF)
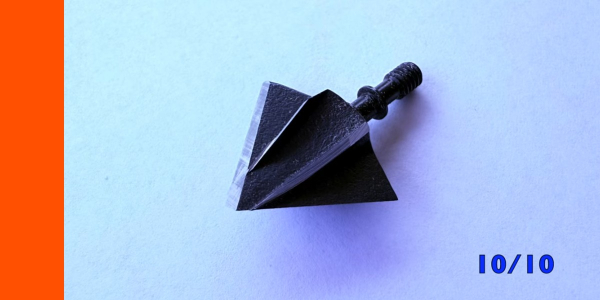
The head is in pristine condition after the 3 shots through the MDF.
Durability Test 2 (2 shots 22 ga Steel Plate)
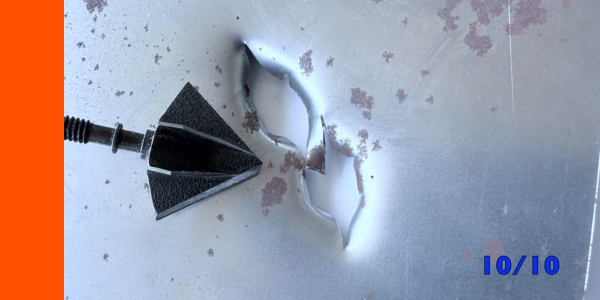
Here is the Katana after the two shots into the steel plate, and the broadhead is just in perfect condition. There are only minor cosmetic scratches on the blades, not to the edge themselves. And then, you can see the holes… man, really nice oval holes. You can even see some of the slits created by those two bleeders on each side to make them extra wide in that way. That’s really cool.
Durability Test 3 (1 Shot Cinder Block)
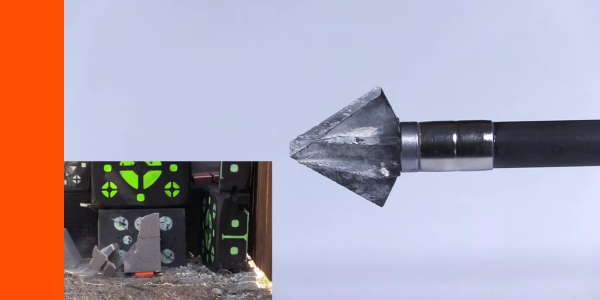
So here’s the Katana after all the durability testing. Of course, it did perfectly well on the MDF and also on the steel plate. You couldn’t even tell it was shot! And then into the cinder block, man, it put the smack down on that cinder block! I’ve seen cinder blocks break before, but usually there’s a big crack and it’s kind of obvious it’s going to happen. This one, I was surprised because I aimed more down low so the top wouldn’t break off, but really impressive and yet still, it’s just in perfect shape, spins perfectly well, edges are in really good shape, and can be used again. It had perfect durability through all these tests.
The Katana… A Record Score!
So what do you think about the Annihilator Katana broadhead?
I had a feeling it was going to do really well. I thought since it had a low profile, it was probably going to fly really well. I also thought that because it had a lot of of cutting surface compact, it would probably be durable and penetrate well. But, I had no idea it was going to do as well as it did!
Early in 2025, I came out with some new bonuses to help separate the really special broadheads from the pact. One of them is if the sharpness and the edge retention tests are both 200 grams of force or under then they get a 2-point bonus, because it’s very rare to have it happen.
Another bonus is if it reaches the maximum penetration of 70 layers of cardboard and 10″ in the gel, MDF, and rubber foam mat tests, it gets a 2-point bonus. That has never happened before now.
Additionally, if it gets a perfect score in durability through the MDF, the steel plate, then the concrete, there’s no deduction. It gets a perfect score and then it gets an extra 2-points. It happens every once in a while and it did with the Katana.
I did not expect one broadhead to get bonuses in all those areas. But, the Katana did. It got the bonus for the sharpness and edge retention. It got the bonus for the penetration, the best penetrating broadhead way through the layers of cardboard and through the gel and MDF and rubber foam mat combo. And it came out looking brand new! I cleaned it off and it looks brand new… incredible!
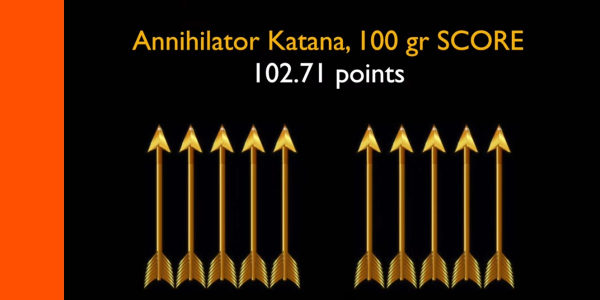
The scorecard for the Katana was… a new record!
So the Katana literally broke the mold. It scored over 100 points. But, even if you remove the 6 points of extra bonus that it got, it still got the highest score of any fixed blade head that I’ve tested by far.
So, let me tell you, this is a really impressive head.
The only knock that I would give on it is I wish it has a little bit wider cutting diameter to make a little bit wider hole. However, I think it more than makes up for that with all the cutting edges with the vacuum. I’m interested in testing the vacuum that it creates. The internal damage, the rotation, and the incredible rotation; I wasn’t expecting all that.
If you’re looking for something to penetrate deeply, or maybe you have a light setup or are hunting a big animal or even you just want to cause massive internal destruction and use a really low profile broadhead, man, this is one really worth considering.
So, what more can I say? What a fantastic broadhead!
